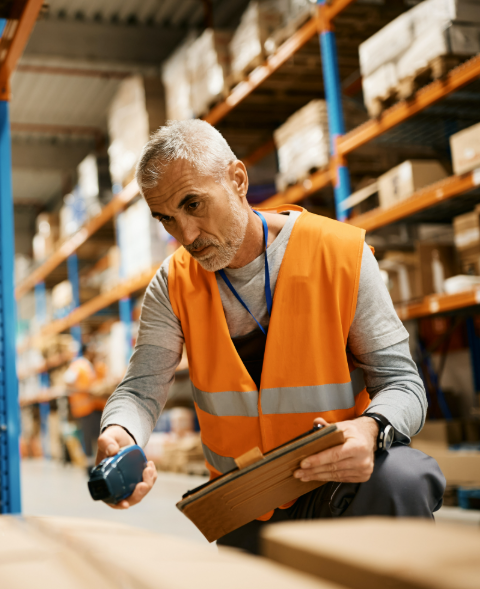
The Importance of Capacity Planning in Supply Chain Management
As businesses face increasing consumer demands and global competition, ensuring operational efficiency is paramount for success. One of the most critical, yet often overlooked, aspects of supply chain management is capacity planning. This strategic process helps businesses forecast their production needs, align resources, and ultimately meet customer demands efficiently.
Effective capacity planning allows companies to optimize their resources, reduce waste, and improve performance, all while keeping costs under control. Let’s dive into why capacity planning is essential for today’s supply chains and how it can be leveraged to drive success.
What is Capacity Planning in Logistics?
Capacity planning in logistics refers to the process of determining the production capacity required to meet fluctuating demand. It involves analyzing how well a company’s existing facilities, workforce, and equipment can accommodate both current and future demands. Proper capacity planning ensures that businesses can fulfill customer orders in a timely manner without overproducing or falling short of demand.
This process isn’t limited to just warehousing or transportation; it covers every area of the supply chain. For example, it involves answering questions like:
- Can our workforce handle demand spikes during peak seasons?
- Do we have enough transportation resources to handle upcoming shipments?
- Can our suppliers meet our demands if we scale up production?
By addressing these questions, capacity planning helps prevent issues like underproduction, stockouts, or delays that could harm the business and its relationships with customers.
Types of Capacity Planning
Capacity planning varies depending on the time frame and needs of the business. The three primary types of capacity planning are:
- Short-term Capacity Planning
This focuses on immediate needs, such as adjusting labor shifts, warehouse space, or delivery routes for daily or weekly demands. It’s highly reactive, aiming to solve issues as they arise, while monitoring fluctuations in orders and inventory levels. - Medium-term Capacity Planning
Looking ahead six months to two years, this type of planning helps companies make decisions regarding workforce hiring, negotiating supplier contracts, or procuring new equipment. It aligns operational capabilities with future sales forecasts, ensuring businesses are prepared for upcoming changes. - Long-term Capacity Planning
Spanning two to five years, this involves strategic decisions like expanding production facilities, acquiring new technologies, or entering new markets. It requires significant investment and detailed forecasting to ensure future growth aligns with the company’s long-term objectives.
Capacity Planning Strategies
To optimize capacity, businesses often use various strategies depending on market conditions. The most common strategies include:
- Lead Strategy
In this approach, businesses add capacity ahead of expected demand increases. It’s a proactive strategy designed to prevent bottlenecks and capitalize on future growth opportunities. While this may require a higher upfront investment, it reduces the risk of missing sales or disappointing customers. - Lag Strategy
A more reactive strategy, the lag approach involves adding capacity only after demand has outpaced existing capabilities. This can reduce the risk of overinvestment but may lead to delays, stockouts, or customer dissatisfaction if not managed carefully. It’s often used in industries with predictable demand and short lead times. - Match Strategy
The match strategy combines elements of both the lead and lag strategies, adding capacity incrementally based on real-time market signals. This flexible approach helps businesses balance demand fluctuations while avoiding overextension. However, it requires constant monitoring and accurate forecasting.
Capacity Planning vs. Resource Planning
While capacity planning and resource planning are closely related, they focus on different aspects of supply chain operations.
- Capacity Planning:
Focuses on ensuring the system’s maximum output capability over a specific time period. It answers questions about whether current resources are sufficient to meet anticipated demand and whether production can scale up accordingly. - Resource Planning:
This is more tactical and involves allocating specific resources (labor, materials, equipment) to meet operational demands. It deals with the day-to-day requirements needed to execute the tasks identified in capacity planning.
In simple terms, capacity planning ensures the business can meet future demand, while resource planning ensures the right resources are in place to achieve that capacity.
Why Capacity Planning Matters
Capacity planning is not just a back-office function but a strategic tool that directly impacts a company’s ability to grow, mitigate risks, and deliver exceptional service. It allows businesses to make informed decisions about production, logistics, and procurement, helping them stay competitive and agile.
Without effective capacity planning, companies risk operating reactively—constantly scrambling to address issues like stockouts, production delays, and rising costs. With a well-executed capacity plan, businesses can avoid these disruptions, optimize their resources, and build a more resilient supply chain.
Conclusion
As consumer expectations and global markets continue to evolve, the need for smart, strategic capacity planning has never been more important. It helps businesses not only anticipate and manage demand but also align their production capabilities with long-term growth goals. Whether you’re focusing on short-term logistics adjustments or making strategic investments for future expansion, capacity planning provides the foundation for sustainable, efficient, and profitable operations.
By embracing capacity planning, supply chain leaders can navigate disruptions more effectively, ensure customer satisfaction, and maintain a competitive edge. It’s time to move beyond reactive problem-solving and adopt a proactive, strategic approach to meeting demand and driving business success.