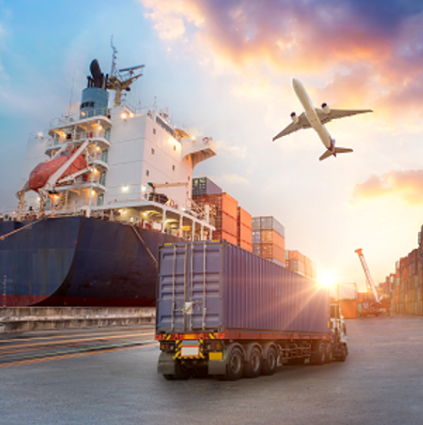
How Nearshoring is Transforming Supply Chains
In recent years, the landscape of global supply chains has been undergoing a significant shift. Traditional supply chain models, particularly the “just-in-time” approach, which focused on rapid delivery with minimal inventory, have been disrupted by unpredictable events such as the COVID-19 pandemic and rising geopolitical tensions. As a result, many businesses are now looking closer to home for manufacturing solutions—enter nearshoring. This trend is reshaping how companies approach production and supply chain resilience, offering numerous benefits that can boost efficiency and reduce risks.
What Is Nearshoring?
Nearshoring involves relocating production or sourcing activities from distant countries to nearby or regional locations. For example, a U.S.-based company might move its manufacturing operations from Asia to Mexico or other Central American countries. This trend is gaining momentum as businesses seek to enhance their supply chain resilience while reducing costs. A report by global management consulting firm Kearney notes that U.S. manufacturing is experiencing a revival, with nearshoring playing a significant role in this shift.
U.S. imports from traditional low-cost countries like China have been on the decline, while imports from Mexico have surged. According to the data, U.S. imports from Mexico have increased by 32% since pre-pandemic levels, a clear indication that companies are shifting their production closer to home. This change is helping businesses rebuild production capacity and reduce their reliance on distant suppliers.
Real-World Examples of Nearshoring in Action
Several prominent companies are already reaping the benefits of nearshoring. For example, U.S. automakers such as Ford and General Motors have shifted production to Mexico to take advantage of lower costs and proximity to their key market. This move allows for faster response times to market demands, lower shipping costs, and reduced risk of supply chain disruptions.
Apple has also embraced nearshoring by moving some of its iPhone 14 production from China to India, a strategy often referred to as “friendshoring.” This approach focuses on moving production to countries that are seen as reliable allies, rather than just geographically closer locations.
By 2023, 42 companies had set up new manufacturing operations in Mexico, with eight of them hailing from the United States, according to ProMexico Industry.
Key Benefits of Nearshoring
Nearshoring offers a variety of advantages that enhance supply chain efficiency:
- Reduced Lead Times: With production closer to the end market, businesses can significantly reduce lead times and better respond to consumer demand. This helps prevent stockouts and ensures products are available when needed.
- Improved Supply Chain Resilience: By diversifying suppliers and reducing dependence on a single distant location, companies can better withstand disruptions. For example, nearshoring mitigates risks from geopolitical instability or natural disasters, ensuring a more stable supply chain.
- Geopolitical and Natural Disaster Protection: Producing goods closer to home shields companies from the risks of international conflicts or trade disruptions. It also provides a buffer against the impacts of natural disasters that can cripple distant supply chains.
Challenges of Nearshoring
While nearshoring offers several benefits, it also comes with challenges. The initial setup costs can be substantial, including investments in infrastructure, technology, and workforce training. Additionally, companies may need to navigate complex regulatory requirements and address potential cultural differences when working with new partners in nearby countries.
To overcome these challenges, businesses should invest in cultural awareness training for their teams and seek legal counsel to help manage regulatory complexities. By addressing these hurdles proactively, companies can unlock the full potential of nearshoring.
How Plastic Pallets Can Support Nearshoring Strategies
Efficient logistics are crucial for successful nearshoring operations. One way to streamline operations is through the use of plastic pallet pooling services. Plastic pallets are more durable, consistent, and easier to maintain than wood pallets, making them ideal for nearshoring activities.
Plastic pallet pooling services can handle the procurement, storage, transportation, and repair of pallets, allowing companies to focus on their core operations. These services also contribute to sustainability efforts, as plastic pallets are reusable and recyclable, supporting environmental goals.
As more businesses turn to nearshoring to stay competitive, adopting plastic pallet pooling can further enhance the efficiency and cost-effectiveness of these strategies.
Conclusion
Nearshoring is quickly becoming a key strategy for businesses looking to improve supply chain resilience and efficiency. By relocating production closer to home, companies can reduce lead times, safeguard against disruptions, and streamline operations. While nearshoring does present challenges, with careful planning and the right logistics solutions, it offers significant advantages that can help businesses remain competitive in an ever-changing global market.