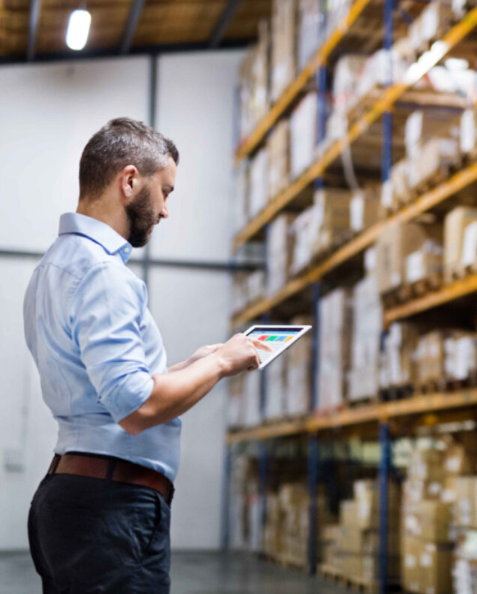
Effective Strategies for Managing Supply Chain Costs
As businesses continue to face rising costs and increased competition, effective supply chain cost management has become essential for staying profitable. From procurement to distribution, every stage of the supply chain involves costs that can quickly add up. In today’s economy, where inflation and consumer demand are constant factors, managing these expenses efficiently is crucial for maintaining competitive pricing and ensuring long-term success.
Breaking Down Supply Chain Costs
Understanding the different components that make up supply chain costs is vital for managing them effectively. These costs typically fall into five main categories:
- Procurement Costs: These are costs associated with acquiring raw materials, components, and services. Fluctuations in material costs can directly impact the final price of products.
- Transportation Costs: Freight, fuel, and warehousing are significant parts of transportation expenses. While costs have been decreasing since the pandemic disruptions, transportation still represents a major share of overall supply chain spending.
- Inventory Holding Costs: These costs cover storage, handling, and potential obsolescence of inventory. Much of this is tied to warehouse operations, including rent, utilities, labor, and equipment.
- Production Costs: This category includes expenses related to manufacturing, including labor, overhead, and equipment.
- Distribution Costs: These costs involve packaging, handling, and order fulfillment, and are separate from transportation-related costs.
By understanding and analyzing these costs, businesses can identify where reductions are possible and implement strategies for improvement.
Key Strategies for Reducing Supply Chain Costs
Effectively managing supply chain costs requires a strategic approach. Here are a few essential methods:
- Accurate Demand Forecasting: Predicting product demand accurately helps prevent overstocking or understocking. Advanced forecasting tools can improve accuracy, allowing for better inventory management.
- Route Optimization: Optimizing transportation routes can significantly reduce fuel consumption, helping to cut costs and improve efficiency.
- Inventory Management Techniques: Practices like Just-In-Time (JIT) inventory, which minimizes stock levels, and Vendor-Managed Inventory (VMI), where suppliers manage inventory, help keep storage and holding costs down.
- Supplier Relationships: Strong supplier partnerships can lead to better pricing and more efficient sourcing, thus reducing procurement costs.
- Adopting Technology: Modern supply chain management depends heavily on technology. Supply chain management software, advanced analytics, and AI are key tools for optimizing operations. For instance, transportation management systems (TMS) can help businesses choose the best routes and carriers, while warehouse management systems (WMS) improve inventory control.
The Importance of Continuous Improvement
In the ever-changing landscape of supply chains, continuous improvement is crucial. Regularly reviewing processes to identify inefficiencies is a fundamental part of cost management. This involves:
- Cost Benchmarking: Comparing your supply chain costs to industry standards helps highlight areas where your business may be underperforming.
- Root Cause Analysis: Investigating the underlying causes of inefficiencies and costs can uncover hidden issues that drive up expenses. Once identified, corrective actions can be taken to address these issues.
- Collaboration Across the Supply Chain: Engaging suppliers, carriers, and partners in cost-reduction initiatives ensures a collaborative effort, leading to shared benefits across the network.
The Role of Plastic Pallet Pooling
A simple yet impactful way to reduce supply chain costs is by using plastic pallet pooling. By partnering with a plastic pallet provider like iGPS, businesses can reduce overhead costs related to procurement, storage, and transportation. The benefits of plastic pallets include:
- Lower Overhead Costs: No need for storing, repairing, or discarding pallets as part of a pooling system.
- Better Automation Compatibility: Plastic pallets are cleaner and smoother, which helps prevent jamming and improves efficiency in automated systems.
- Improved Worker Safety: Lighter than wood pallets and free from nails and splinters, plastic pallets reduce workplace injuries and lost productivity.
- Fuel and Environmental Savings: Their lighter weight leads to less fuel consumption during shipping, ultimately reducing greenhouse gas emissions.
- Easier Cleaning: The non-porous surface of plastic pallets makes them easier to clean and sanitize compared to wood, reducing the risk of contamination.
Conclusion
Supply chain cost management is essential for businesses aiming to remain competitive in an increasingly challenging market. By focusing on accurate demand forecasting, optimizing routes, and leveraging technology, businesses can reduce operational expenses. Additionally, switching to solutions like plastic pallet pooling can make a significant impact on costs and improve overall supply chain efficiency. Companies that prioritize continuous improvement and cost optimization will be well-positioned for long-term success in the global marketplace.