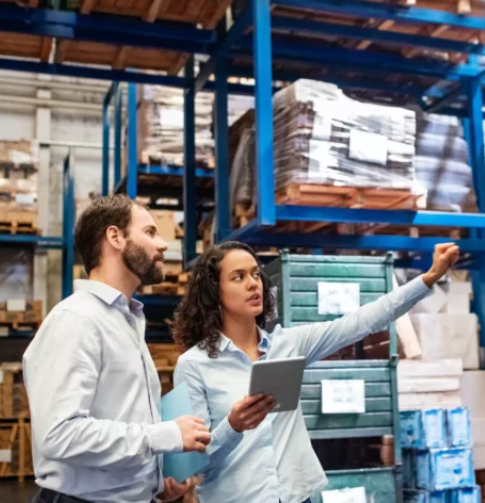
Effective Inventory Planning for Supply Chain Optimization
Effective inventory planning is a key element of a well-optimized supply chain. For businesses in various industries, managing inventory with precision ensures that customers and retailers alike have access to the right products at the right time. However, developing an effective inventory management strategy requires understanding various models and methodologies. These techniques help businesses meet customer demand while preventing shortages, excess stock, and the challenges of inventory holding costs.
What is Inventory Planning?
Inventory planning is the process of determining the optimal quantity and timing of stock to meet customer demand, align with production schedules, and achieve business objectives. It involves forecasting future inventory needs, setting targets, and establishing clear guidelines on when to restock.
When done right, inventory planning helps businesses maintain the right balance of stock, avoiding overstocking, which ties up capital, or understocking, which risks lost sales and customer dissatisfaction. The ultimate goal is to align supply with demand while optimizing operations and reducing costs.
Key Inventory Planning Methods
There are several inventory planning models that cater to different operational needs. Some of the most popular methods include:
1. Economic Order Quantity (EOQ)
The EOQ model calculates the ideal order size that minimizes the total cost of inventory, including ordering and holding costs. This model is best for businesses with stable demand and high-volume products. It allows for cost-effective inventory management by determining the most efficient order quantity.
2. ABC Analysis
This method divides inventory into three categories:
- A items: High-value, low-quantity items that need tight control.
- B items: Medium-value items with moderate sales volume.
- C items: Low-value, high-quantity products requiring less oversight.
ABC analysis helps businesses focus their resources and inventory management efforts on the most critical items.
3. Just-in-Time (JIT) Inventory
JIT is a lean inventory system that ensures stock arrives exactly when it is needed for production or sale. While JIT minimizes holding costs and waste, it also requires dependable suppliers and precise demand forecasting. This method works best in stable environments where demand is predictable.
4. FIFO & LIFO Inventory Models
These models determine how inventory costs are recorded and goods are sold:
- FIFO (First-In, First-Out): Older inventory is used or sold first, ideal for perishable goods like food products.
- LIFO (Last-In, First-Out): Newer stock is sold first, useful for tax advantages in inflationary environments, though it may not reflect the actual physical flow of products.
5. Deterministic Inventory Model
This method assumes constant demand and lead times, making it ideal for simple reorder strategies in predictable conditions. It’s a useful tool for modeling scenarios in environments with consistent supply and demand.
6. Work in Progress (WIP) Inventory
WIP refers to goods that are partway through the production process. Managing WIP effectively ensures that raw materials, labor, and production capacity are balanced, preventing bottlenecks and inefficiencies.
7. Perpetual Inventory Model
A real-time tracking system that continuously updates inventory records through technology like RFID or barcode scanning. This model provides businesses with up-to-the-minute visibility into stock levels, facilitating dynamic decision-making.
8. Minimum Order Quantity (MOQ)
This model determines the smallest amount a supplier will sell. Planners must account for MOQs when making purchasing decisions, especially when balancing cost savings against space limitations or low demand forecasts.
9. Reorder Point (ROP) Model
The ROP model establishes the inventory level at which restocking should occur, factoring in current stock levels, lead time, and demand rate. It’s particularly useful in environments where demand fluctuates, and safety stock is needed to mitigate uncertainties.
Benefits of Effective Inventory Planning
Well-executed inventory planning offers numerous advantages for businesses:
- Cost Reduction: By balancing stock levels, businesses can avoid the expenses of excess inventory, including storage, insurance, and depreciation. Methods like EOQ and JIT help streamline operations, reducing costs significantly.
- Improved Cash Flow: By minimizing capital tied up in inventory, businesses can allocate funds to growth opportunities, research, and debt reduction.
- Enhanced Customer Satisfaction: Reliable stock levels reduce the risk of stockouts, ensuring customers receive their orders promptly and increasing brand trust and loyalty.
- Accurate Forecasting: Better inventory planning leads to more precise demand forecasting, helping businesses make informed decisions, anticipate needs, and adjust operations accordingly.
- Increased Operational Efficiency: Optimized inventory directly impacts procurement, production scheduling, and warehouse management, enhancing the overall performance of the supply chain.
- Stronger Supplier Relationships: Consistent inventory needs allow businesses to negotiate favorable terms, improve pricing, and reduce lead times with key suppliers.
Challenges in Inventory Planning
Despite its many benefits, inventory planning presents challenges for supply chain professionals:
- Demand Fluctuations: Accurately forecasting demand remains difficult due to factors such as economic shifts, seasonality, and changing consumer preferences.
- Supply Chain Disruptions: Events like natural disasters or geopolitical issues can disrupt supply chains, rendering even the best-planned inventory strategies ineffective.
- Data Accuracy: Inconsistent or outdated data can lead to poor decision-making. Maintaining real-time, accurate data is essential for effective inventory management.
- SKU Proliferation: Managing an expanding range of SKUs can complicate inventory planning. Techniques like ABC analysis and perpetual inventory systems can help, but sophisticated tools are required for managing a large variety of products.
- High Holding Costs: Misjudging inventory levels can result in high storage and insurance costs. Inventory planning must strike a balance to avoid overstocking while meeting demand.
- Integration with Other Functions: Inventory planning must align with procurement, sales, and production teams. Any misalignment leads to inefficiencies and disruptions across the supply chain.
Conclusion
Inventory planning is both an art and a science, requiring the use of analytics, forecasting, and collaboration. By implementing effective methods like EOQ, JIT, and Reorder Point models, businesses can optimize their supply chains, improve cash flow, and enhance customer satisfaction. However, successful inventory planning requires constant attention to detail, real-time data, and an understanding of potential challenges. When done well, it helps businesses reduce costs, maintain smooth operations, and stay competitive in a rapidly evolving market.