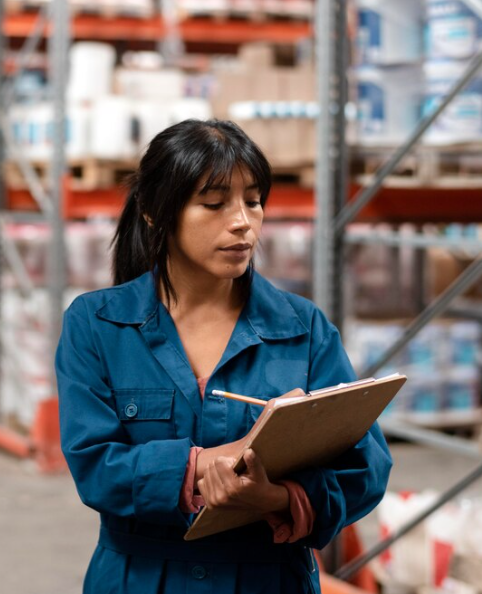
Best Practices for Optimizing Warehouse Management and Inventory Operations
In today’s fast-paced supply chain environment, optimizing warehouse management and inventory operations is crucial to ensuring business success. With rising consumer demands and increasingly complex logistics, organizations must streamline their processes to stay ahead of the competition. Efficient warehouse operations not only guarantee on-time order fulfillment but also enhance accuracy, reduce costs, and ensure a safer working environment.
Understanding Warehouse Inventory Management
Warehouse inventory management involves the coordination and oversight of goods as they move in and out of a facility. This includes monitoring inventory levels, optimizing the warehouse layout, and managing the storage and retrieval of products. Effective management ensures that the right products reach customers at the right time, avoiding stockouts or excess inventory. Moreover, it promotes a strategically organized environment that balances space and stock for optimal efficiency.
Key Warehouse Management Best Practices
- Design a Strategic Warehouse Layout
A well-planned warehouse layout boosts operational efficiency by reducing unnecessary travel time and space. It’s important to organize areas for receiving, storage, picking, packing, and shipping. High-demand items should be placed in easily accessible zones, and vertical space should be fully utilized. This approach minimizes bottlenecks and streamlines material flow.
- Utilize an Advanced Warehouse Management System (WMS)
A robust WMS is the foundation of any modern warehouse. It provides real-time visibility into inventory, automates processes, and tracks orders from receipt to shipment. An ideal WMS integrates smoothly with other supply chain systems and scales with the growth of operations. This system helps increase accuracy, reduce human errors, and empower faster decision-making.
- Implement Accurate Inventory Tracking
Real-time tracking technologies, such as barcodes, RFID, and QR codes, enable efficient inventory management at the SKU level. By automating tracking, these tools minimize errors and provide detailed movement history. Accurate tracking ensures that supply chain managers always know the stock status, preventing issues like stockouts and overstocking.
- Set Clear Inventory Control Policies
Establishing well-defined inventory control policies is essential for minimizing waste and optimizing cash flow. These policies should outline stock level thresholds, reordering protocols, and product handling procedures. For perishable items, using FIFO (First In, First Out) or FEFO (First Expired, First Out) systems helps ensure product freshness and reduces loss.
- Conduct Regular Audits and Cycle Counts
Routine audits and cycle counts verify that physical inventory matches recorded stock. Cycle counting, which involves counting different items at scheduled intervals, is less disruptive than full inventory counts. By regularly checking fast-moving or high-value products, managers can identify discrepancies before they cause significant issues.
- Prioritize Safety in the Warehouse
Safety is a fundamental element of a productive warehouse environment. Compliance with safety regulations, such as OSHA guidelines, and consistent training in equipment use and personal protective equipment (PPE) are essential. Regular safety audits, equipment inspections, and clear walkways contribute to a safer workspace, reducing risks and downtime due to accidents.
- Leverage Automation for Increased Efficiency
Automation tools, such as Automated Storage and Retrieval Systems (ASRS), robotic systems, and automated labeling, significantly enhance speed and consistency while reducing the need for manual labor. Implementing automated processes for tasks like sorting and picking can lead to lasting improvements in efficiency and a solid return on investment.
- Use Data Analytics for Informed Decisions
Data analytics can transform warehouse operations by providing actionable insights. Key performance indicators (KPIs) like order accuracy, space utilization, and picking efficiency allow managers to identify areas for improvement. Predictive analytics also help forecast demand and optimize stock levels, reducing the need for guesswork.
- Improve Order Picking Efficiency
Order picking is one of the most labor-intensive tasks in a warehouse. Optimizing the process by implementing strategies like “wave picking” or “cluster picking” can streamline operations. Tools such as pick-to-light or voice-directed picking systems further enhance speed and accuracy, ultimately leading to better customer satisfaction.
- Streamline Receiving and Shipping Processes
Efficient receiving and shipping are crucial to the smooth operation of a warehouse. Standardizing receiving protocols with detailed checklists ensures that incoming goods are inspected and properly documented. For shipping, automating label generation and optimizing packaging procedures can minimize delays and improve overall throughput.
- Maintain Equipment Regularly
Warehouse equipment, such as forklifts and pallet jacks, must be kept in good condition to ensure smooth operations. A scheduled preventive maintenance plan helps reduce the likelihood of unexpected breakdowns. Keeping a maintenance log and ensuring staff members are trained to report issues promptly can prevent costly repairs.
- Invest in Continuous Staff Training
A well-trained workforce is key to efficient warehouse operations. Providing ongoing training for employees on procedures, equipment handling, and safety protocols enhances productivity and reduces errors. A culture of cross-training increases workforce flexibility, while recognizing top performers fosters a sense of accountability and pride.
- Foster Effective Communication
Clear communication is essential for smooth warehouse operations. Tools like mobile apps and communication systems ensure that employees receive real-time updates on tasks and inventory changes. Effective communication during shift changes and handoffs is also vital to prevent misunderstandings and ensure a collaborative work environment.
- Optimize Storage Capacity
Efficient storage management ensures that warehouse space is utilized to its fullest potential. Employing the right racking systems and assigning items based on their size, weight, and frequency of access can improve space usage. Regularly evaluating storage density and adjusting layouts as needed ensures maximum capacity without sacrificing accessibility.
- Adopt Plastic Pallets for Sustainability and Efficiency
Plastic pallets are a durable and environmentally friendly alternative to traditional wood pallets. They offer greater resistance to moisture and contaminants and are more compatible with automated systems. Their uniformity reduces wear and tear, ultimately contributing to a more sustainable and efficient operation.
By incorporating these warehouse management best practices, companies can enhance their operational efficiency, reduce costs, and provide superior customer service. As consumer expectations and market competition continue to evolve, ongoing improvements in warehouse operations will be crucial for long-term success.