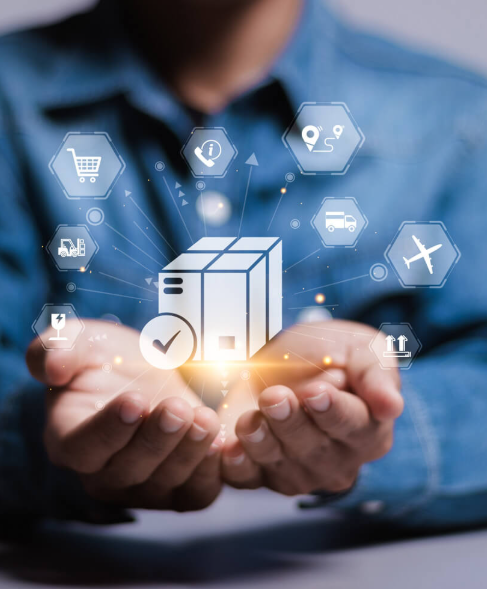
The Role of Aftermarket Logistics in Supply Chain Success
In the world of supply chain management, aftermarket logistics is often overlooked, but it plays a crucial role in ensuring long-term customer satisfaction and operational efficiency. This sector covers everything that happens after a product is sold, from spare parts distribution to warranty and repair services. While many businesses focus on the initial sale, a strong aftermarket logistics strategy can enhance customer loyalty, open new revenue streams, and strengthen the brand’s reputation.
What Exactly is Aftermarket Logistics?
Aftermarket logistics involves the activities that occur after a product has been sold. These include the supply of replacement parts, maintenance and repair services, and ongoing customer support throughout the product’s lifespan. Unlike the initial logistics focused on manufacturing and delivery, aftermarket logistics centers around maintaining the product’s functionality and satisfying customers over time.
Key elements of aftermarket logistics include:
- Parts Distribution: Ensuring replacement parts are readily available for repairs or upgrades.
- Maintenance and Repair Services: Offering services that prolong the product’s useful life.
- Customer Support: Managing warranties, handling returns, and offering technical assistance to keep customers satisfied.
In industries like automotive, electronics, and appliances, the aftermarket is not just a secondary service—it’s a vital revenue source and a chance to nurture lasting customer relationships.
Critical Processes in Aftermarket Logistics
Successful aftermarket logistics is built on several key processes that ensure timely and efficient delivery of products and services:
- Inventory Management: Managing stock levels to meet demand without overstocking or understocking is essential. Advanced systems help optimize inventory using historical data and predictive analytics.
- Order Fulfillment: Efficient order processing ensures quick delivery of parts and services. Streamlining picking, packing, and shipping minimizes delays and errors.
- Distribution Network Optimization: A well-organized network of warehouses and cross-docking facilities helps reduce shipping times and improve customer satisfaction.
- Reverse Logistics: Handling returns, repairs, and recycling in an efficient manner helps recover value from returned goods and supports sustainability.
- Customer Service Integration: A smooth link between logistics operations and customer service ensures prompt responses to inquiries, tracking, and service issues, reinforcing trust in the brand.
Each of these processes contributes to a streamlined aftermarket logistics operation that maximizes efficiency and customer service.
How to Build an Effective Aftermarket Logistics Strategy
To create a robust aftermarket logistics strategy, businesses must focus on technology, process improvement, and careful planning. Key steps include:
- Assess Current Processes: Analyze your existing operations to identify areas for improvement. Use data analytics to pinpoint inefficiencies and set performance benchmarks.
- Invest in Technology: Implement modern tools like warehouse management systems (WMS), transportation management systems (TMS), and predictive analytics to improve efficiency and accuracy.
- Enhance Visibility and Communication: Use systems that provide end-to-end visibility throughout the supply chain. Real-time tracking and communication platforms improve transparency and allow quick issue resolution.
- Form Strong Partnerships: Build collaborative relationships with suppliers, service providers, and logistics partners to streamline operations and reduce lead times.
- Commit to Continuous Improvement: Periodically review performance and adapt strategies based on customer feedback and evolving needs. Lean logistics and Six Sigma methodologies can help refine operations over time.
By focusing on these strategies, companies can build a resilient aftermarket logistics operation that supports customer loyalty and offers a competitive edge.
Strategies for Manufacturers to Improve Aftermarket Logistics
Manufacturers can face unique challenges in aftermarket logistics, but several strategies can help them optimize this area:
- Modular Product Design: Creating products with interchangeable parts simplifies maintenance and repair, improving inventory management and reducing service time.
- Integrated Service Platforms: Digital platforms that track product usage and service records provide predictive maintenance insights, helping address issues before they escalate.
- Strategic Partnerships: Collaborating with third-party service providers and logistics experts can expand a manufacturer’s reach and enhance service delivery.
- Customized Service Contracts: Offering tailored service agreements ensures customer satisfaction by aligning services with specific needs, while also providing a reliable revenue stream.
- Sustainability Initiatives: Implementing environmentally friendly practices, such as recycling programs, can improve a manufacturer’s reputation in an eco-conscious market.
The Role of Plastic Pallet Pooling in Aftermarket Logistics
An innovative trend in aftermarket logistics is the use of plastic pallet pooling. While wooden pallets have been a standard for years, plastic pallets offer distinct advantages:
- Durability and Longevity: Plastic pallets last longer than wood pallets, reducing replacement costs and ensuring consistent performance over time.
- Hygiene and Safety: Plastic pallets are easy to clean, resist moisture, and do not harbor bacteria, making them ideal for industries where hygiene is critical.
- Cost Efficiency Through Pooling: Plastic pallet pooling allows multiple manufacturers to share pallets, reducing costs related to storage, maintenance, and repairs.
- Sustainability: With their durability and recyclability, plastic pallets are an eco-friendly option that helps businesses reduce their carbon footprint.
- Enhanced Tracking and Management: Many plastic pallets, such as those from iGPS Logistics, come with RFID technology, which enables real-time tracking and integration with automated systems.
Incorporating plastic pallet pooling into an aftermarket logistics strategy can help businesses improve efficiency, sustainability, and tracking capabilities.
Conclusion
Aftermarket logistics is an essential part of today’s supply chain, providing significant opportunities for customer retention, revenue generation, and brand enhancement. Whether you are a manufacturer looking to extend the life of your products or a supply chain manager aiming to streamline operations, building an effective aftermarket logistics strategy is crucial. By optimizing processes, leveraging technology, and forming strategic partnerships, businesses can turn post-sale support into a powerful competitive advantage.